Background
Spacesuit is custom built to fit one astronaut. This makes the manufacturing process long and costly. So what if we designed a spacesuit that can fit astronauts in all shapes and sizes? To answer this question, Michael Lye, RISD professor and NASA Coordinator worked along with several RISD students. The suit fits people between 5' 2" to 6' 3" and allows astronauts to don it (put on) easily and move with agility.
Reflection
As the project's research assistant & designer, I manufactured, 3D model, print and finalized the life support systems and durability so it can withstand vigorous Mars simulation tests in extreme environments. Being my first project that was truly 'human centered' design, I became mesmerized by this new style of design that focused on the users.
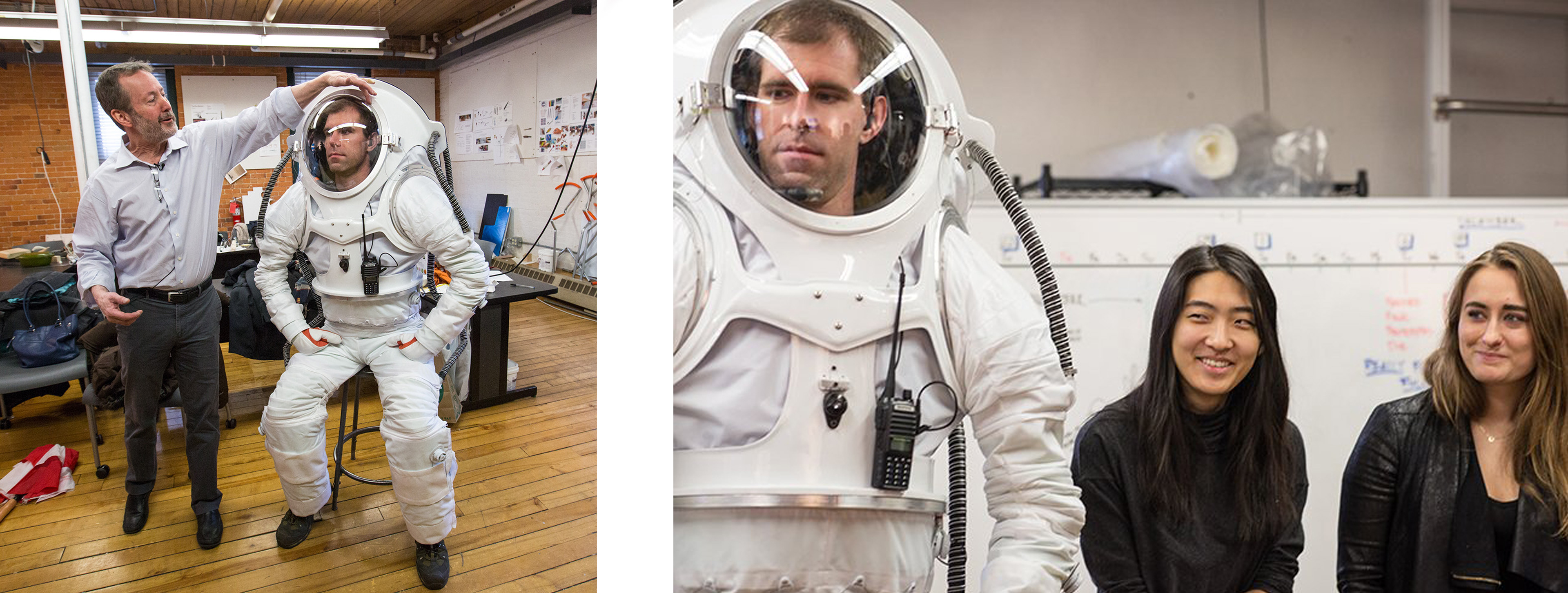
Prof. Michael Lye with the space suit (Left) / Students Ericka Kim and Kasia Matlak (Right)
Space Suit Interior Air Flow System.
The airflow system not only helps cool the astronaut's temperature down, but it also simulates suit pressurization so astronauts can simulate Mars exploration on a simulation site. After attaching the fan, I 3D printed custom connectors and wax bent pipes to evenly distribute airflow to each limbs and the face of the astronaut.
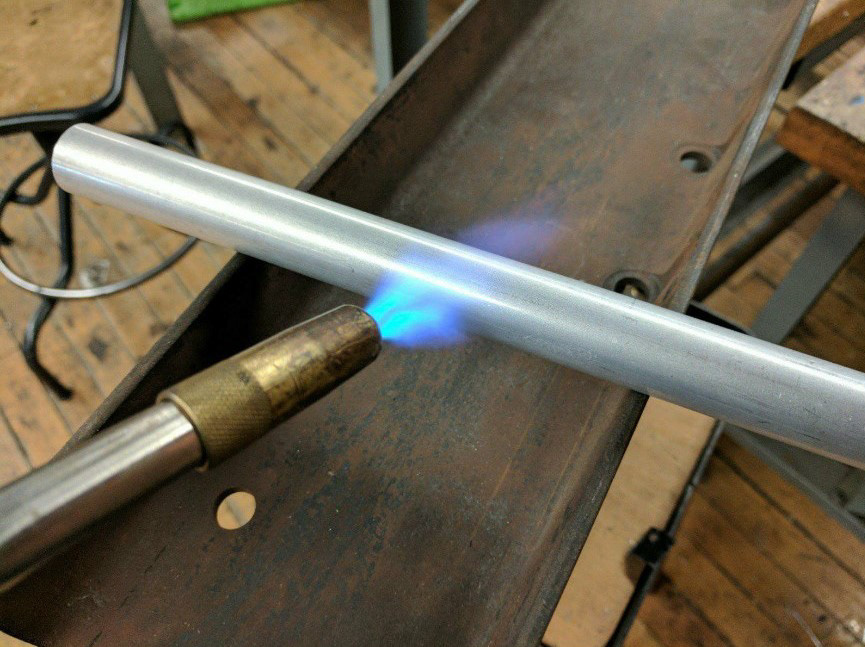
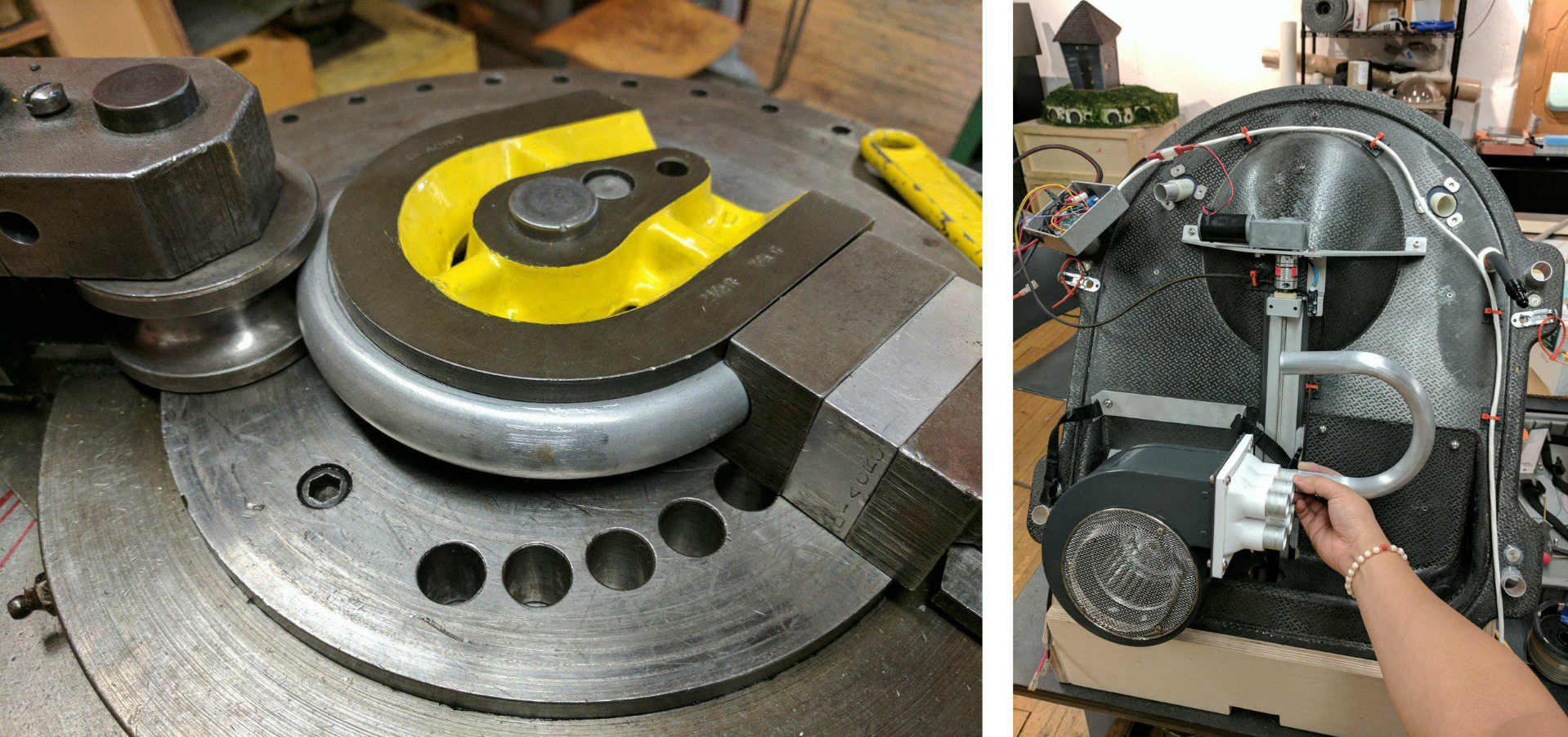
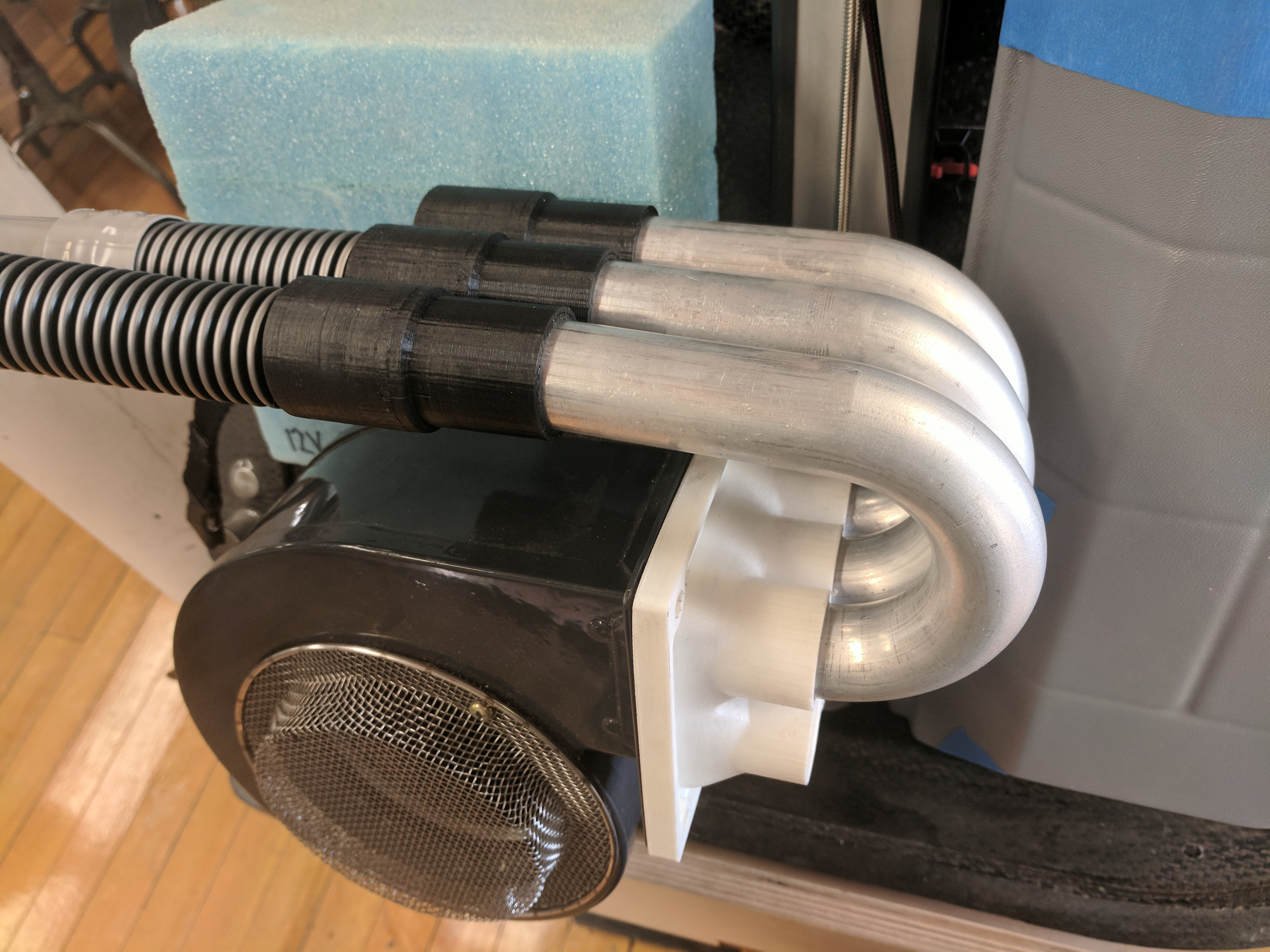
Water Vessel Container
I built a custom designed casing to protect the insulated cooling vessel. The vessel connects to a cooling vest which astronauts will don while putting on the suit. MDF was machined to shape and after a resin coat seal, I vacuum formed polystyrene over the model and test-fitted the cooling bag.
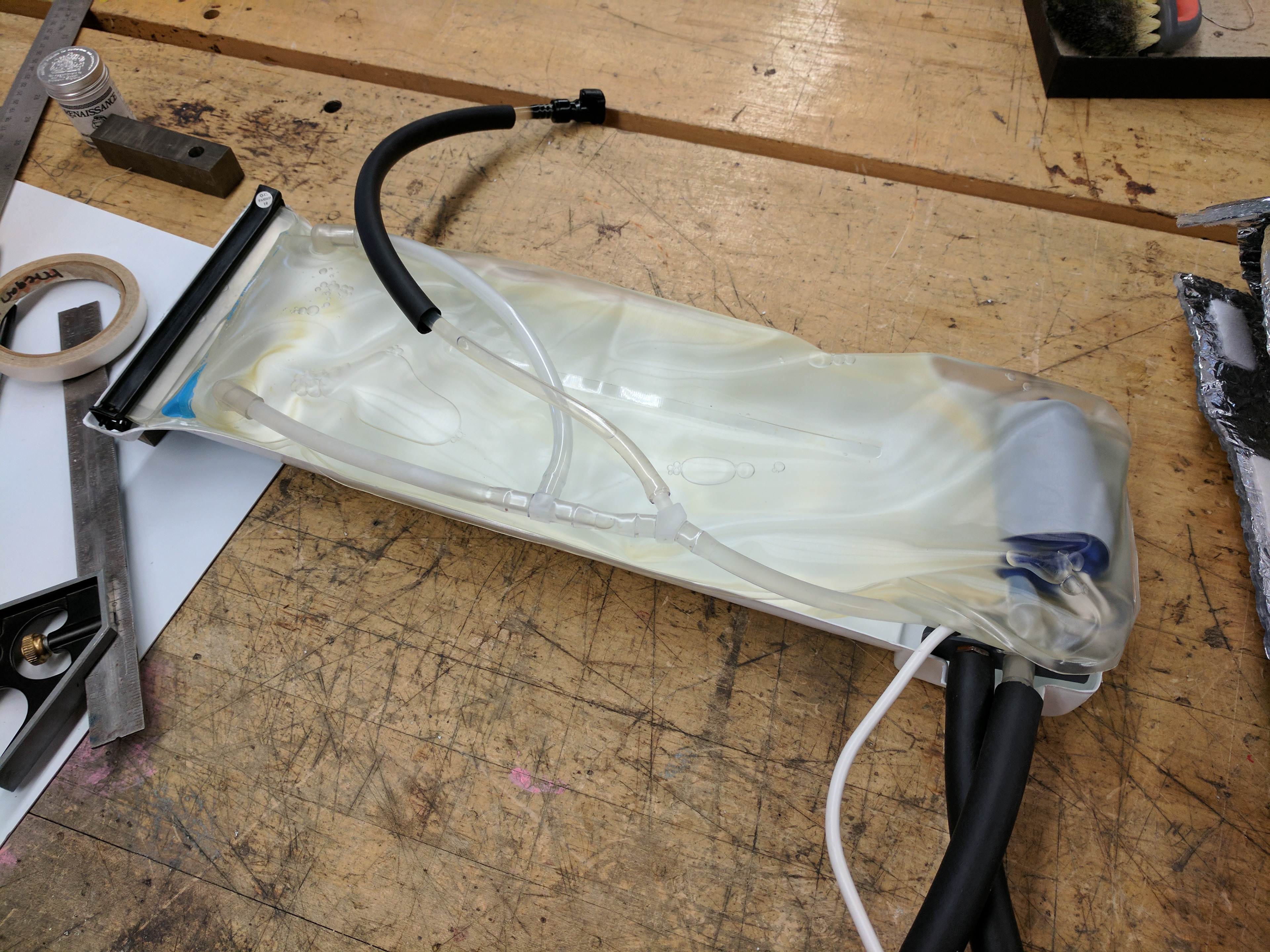
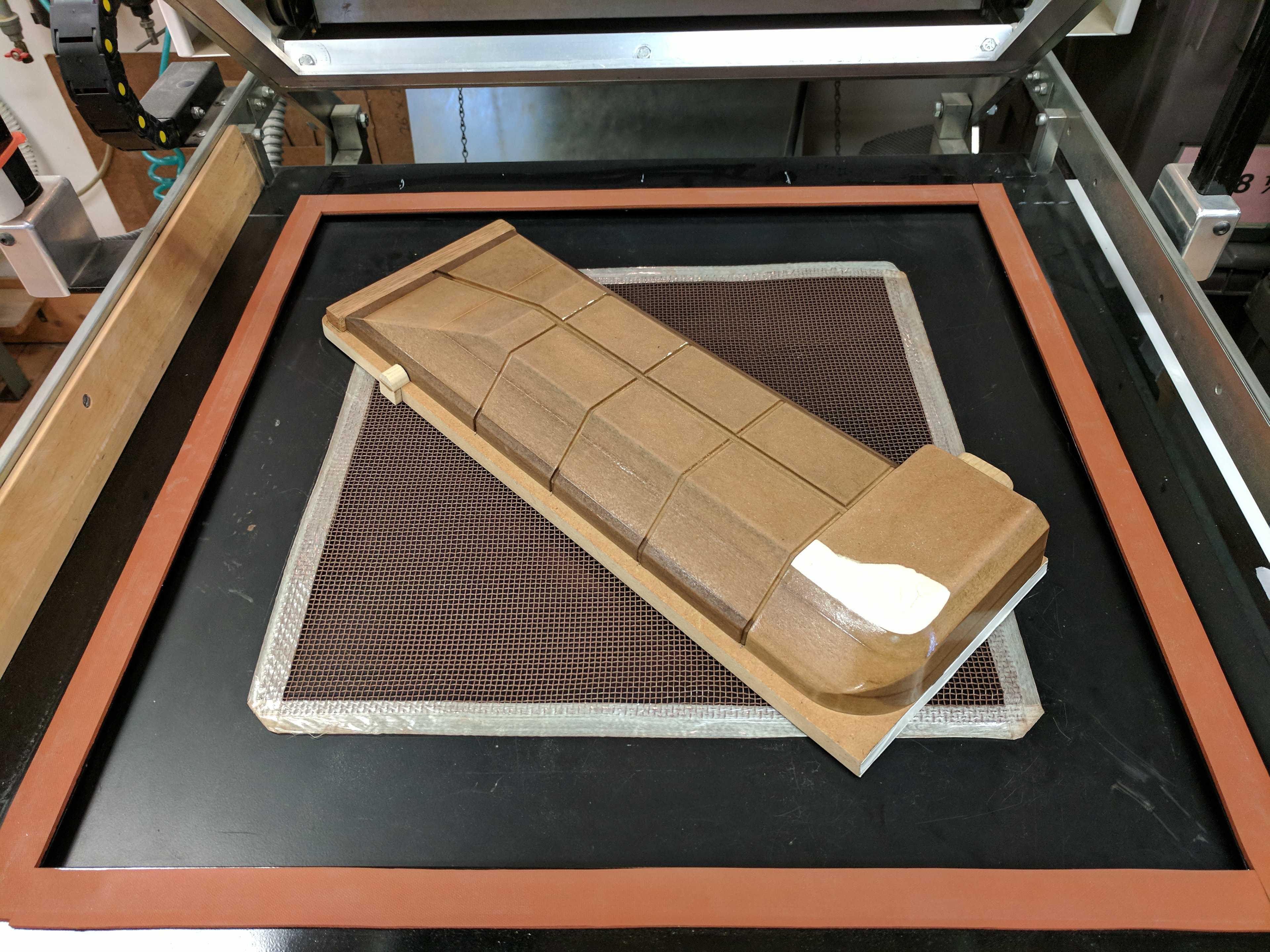
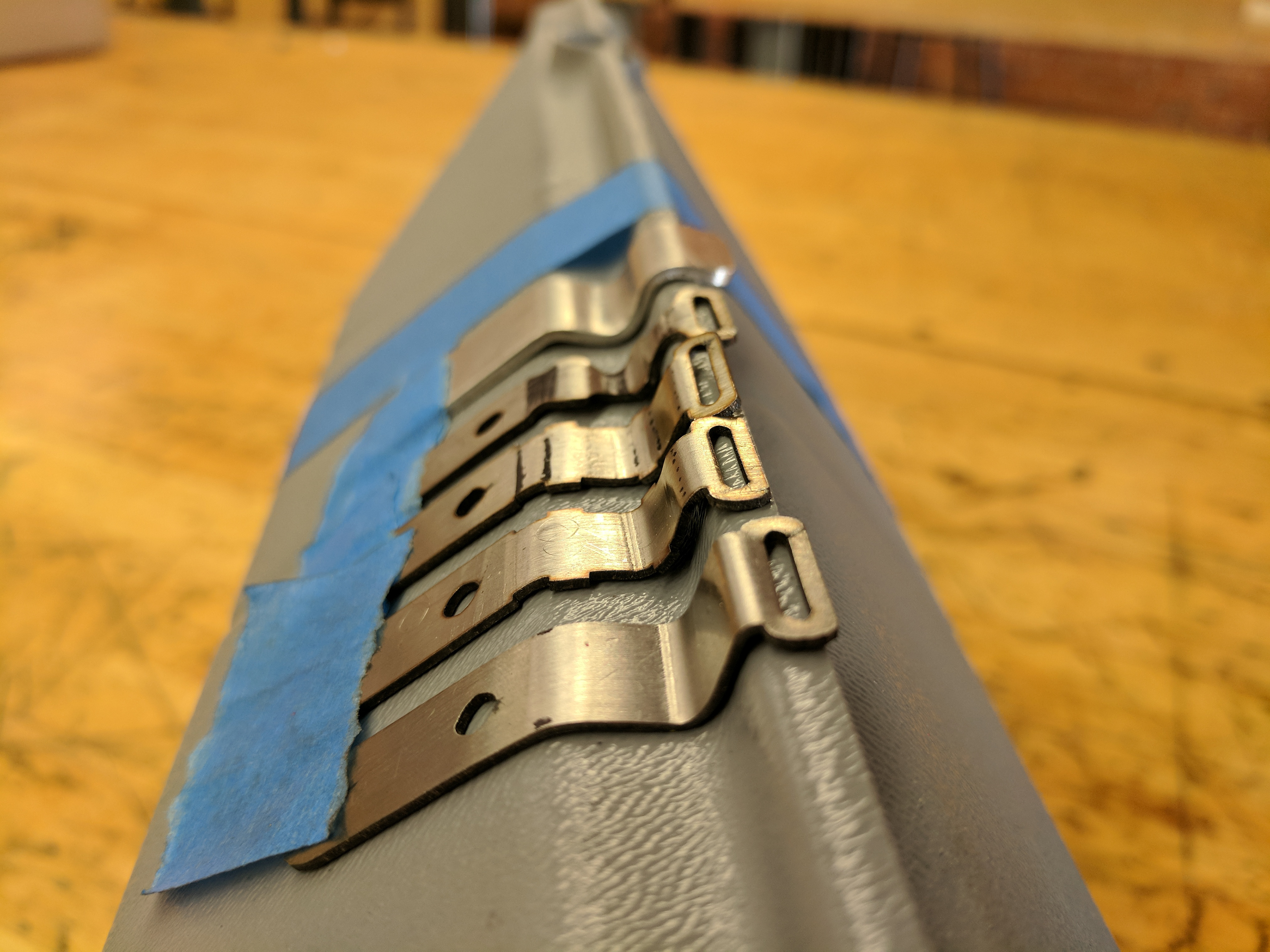
Space Suit Donning Suit
I conducted user tests to understand how people put on the suit. it turns out without a visual indication of front and back on the pants of the suit, many users were confused as to which way they go on.
I solved the problem by making slots on the aluminum waist ring and inserted a sign indicating the front of the space pants. The visual signs were made out of colored acrylic, red indicating left and green indicting right. A MDF jig was machined to create a slot to locate the aluminum ring on the Bridgeport.
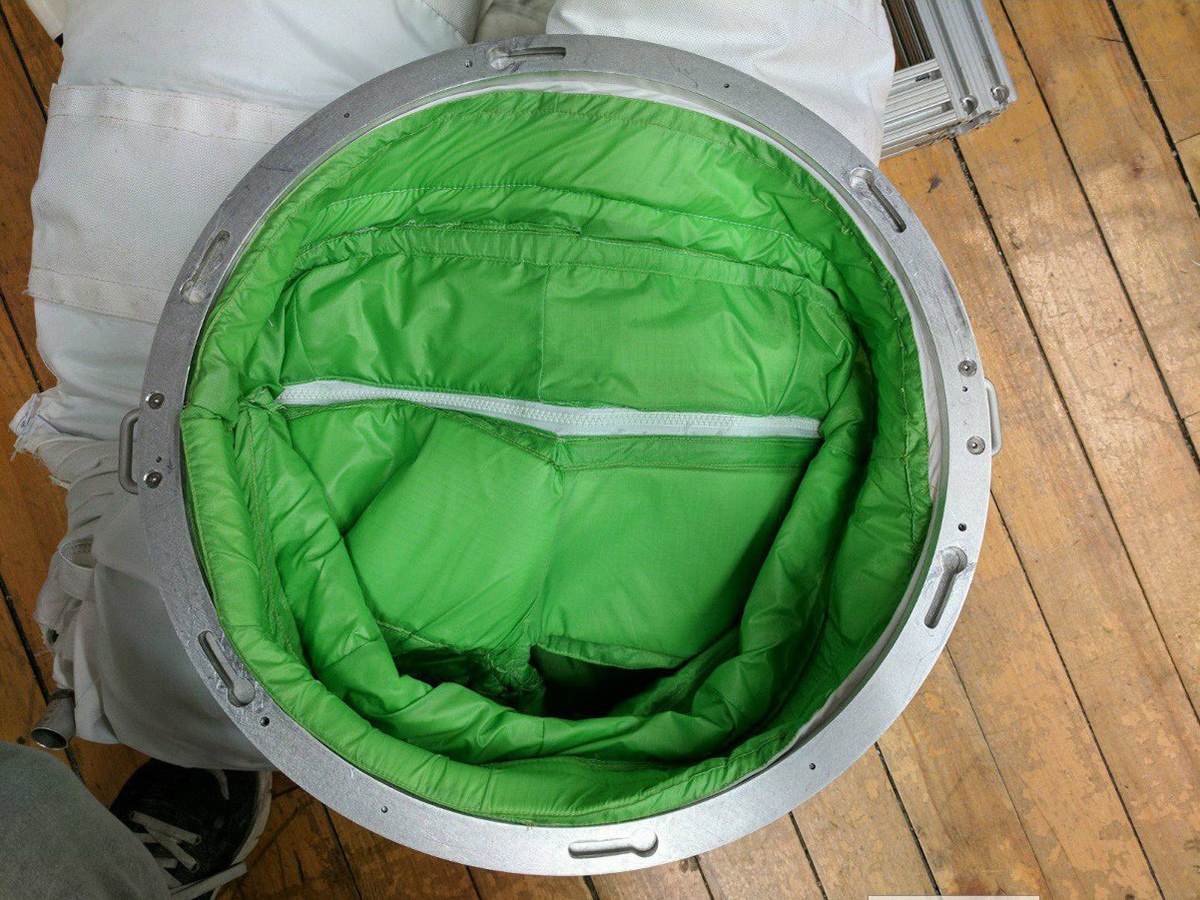

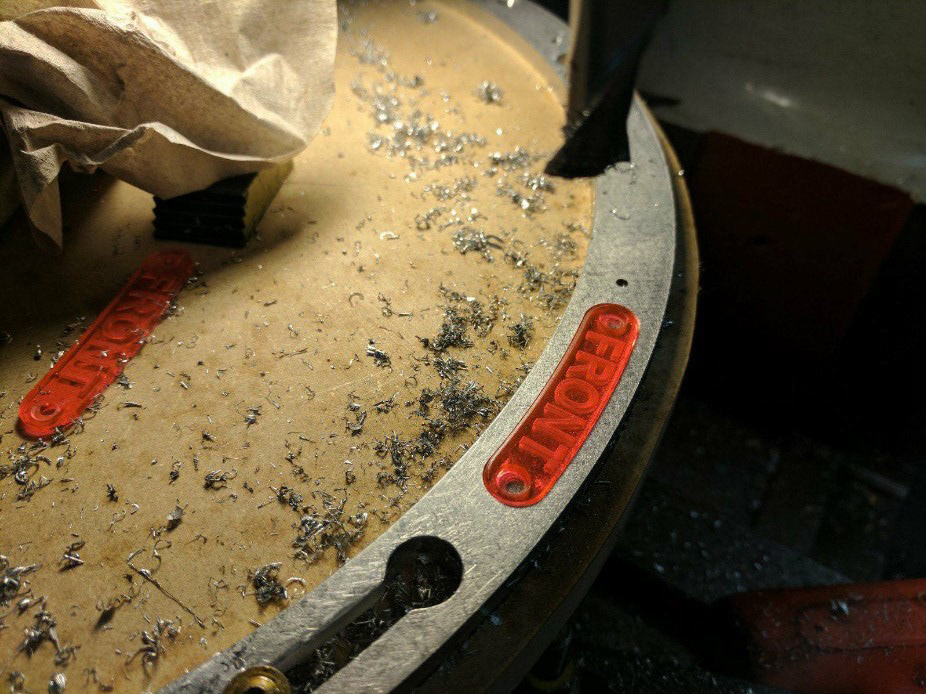
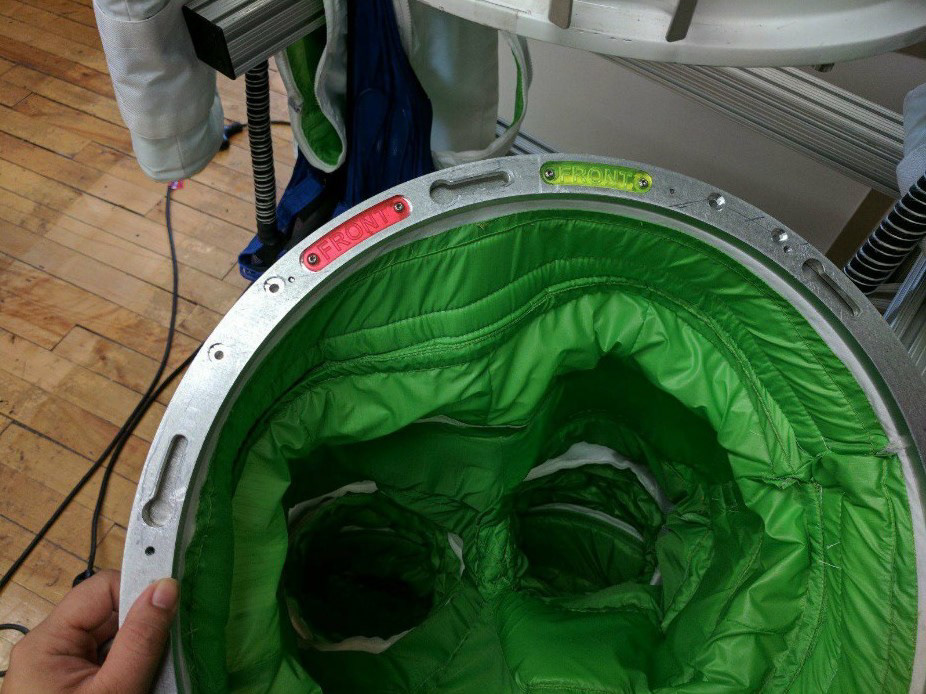
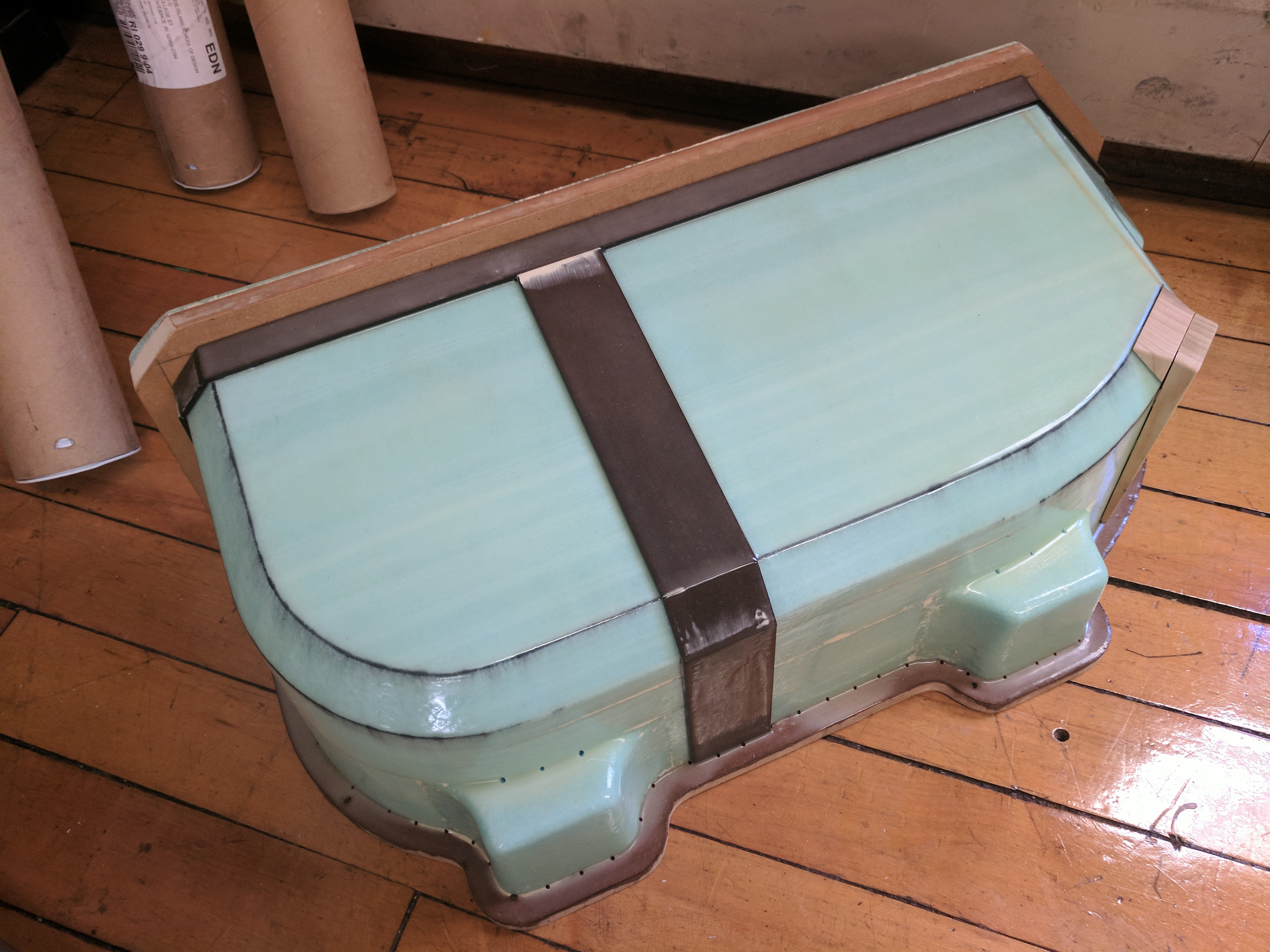
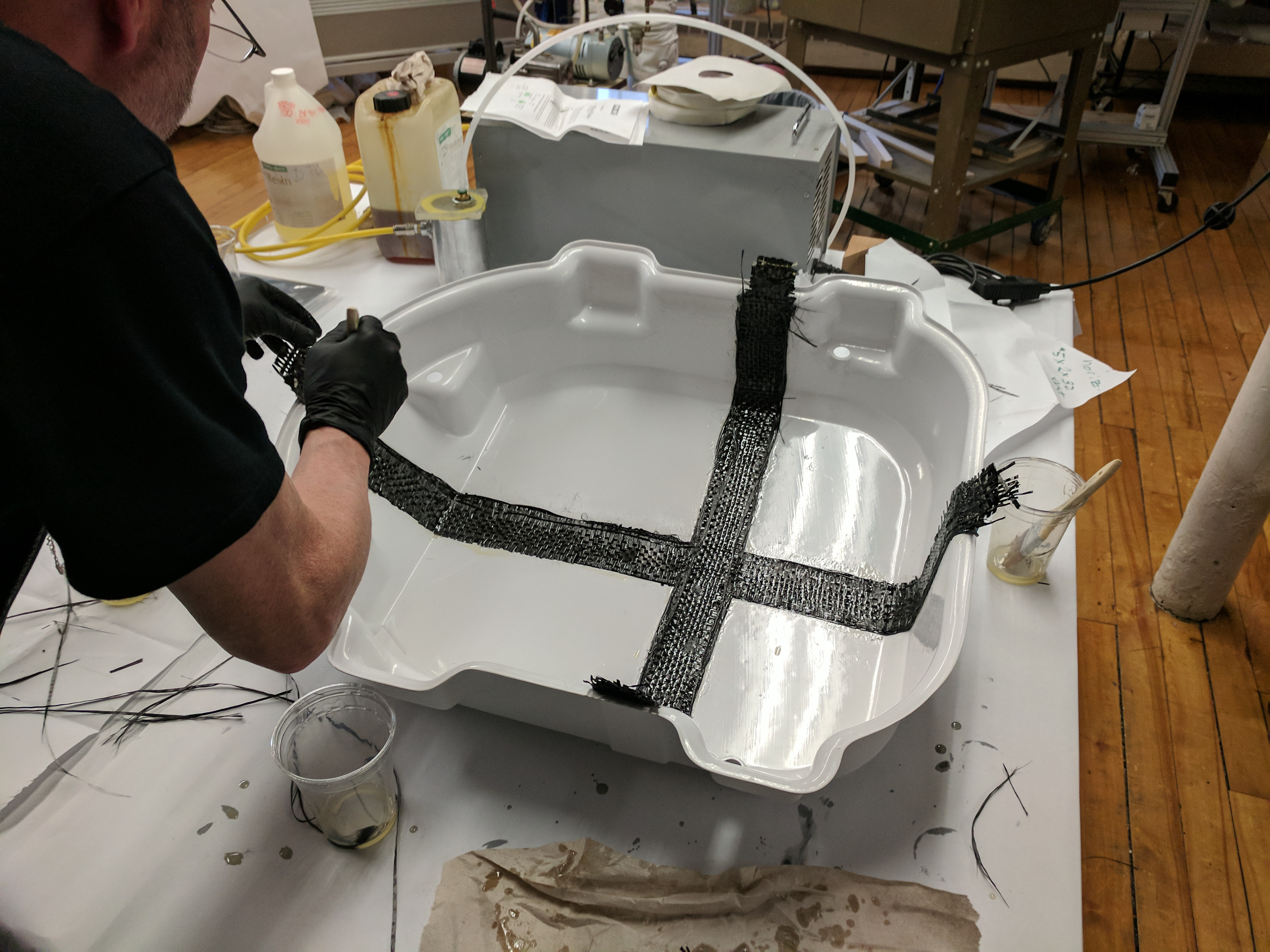
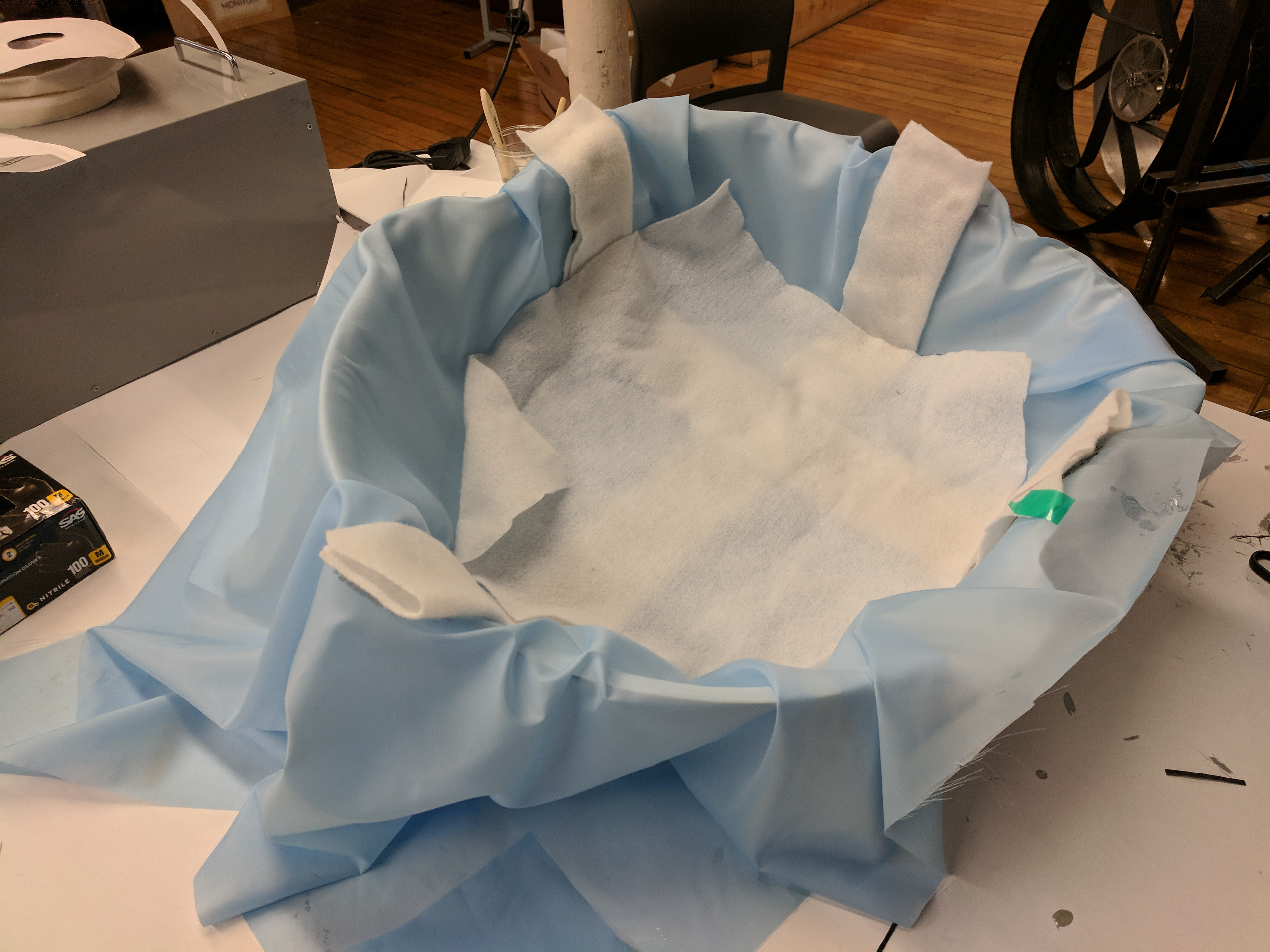
Space Suit Shell
A shell is necessary to protect the support systems installed on the carbon fiber backing of the suit. Like the cooling vessel, the shell was molded with foam and MDF and vacuumed form with textured polystyrene sheet. In order to secure the shell to the backing, custom jigs were made to locate the pins and clips of the shell.
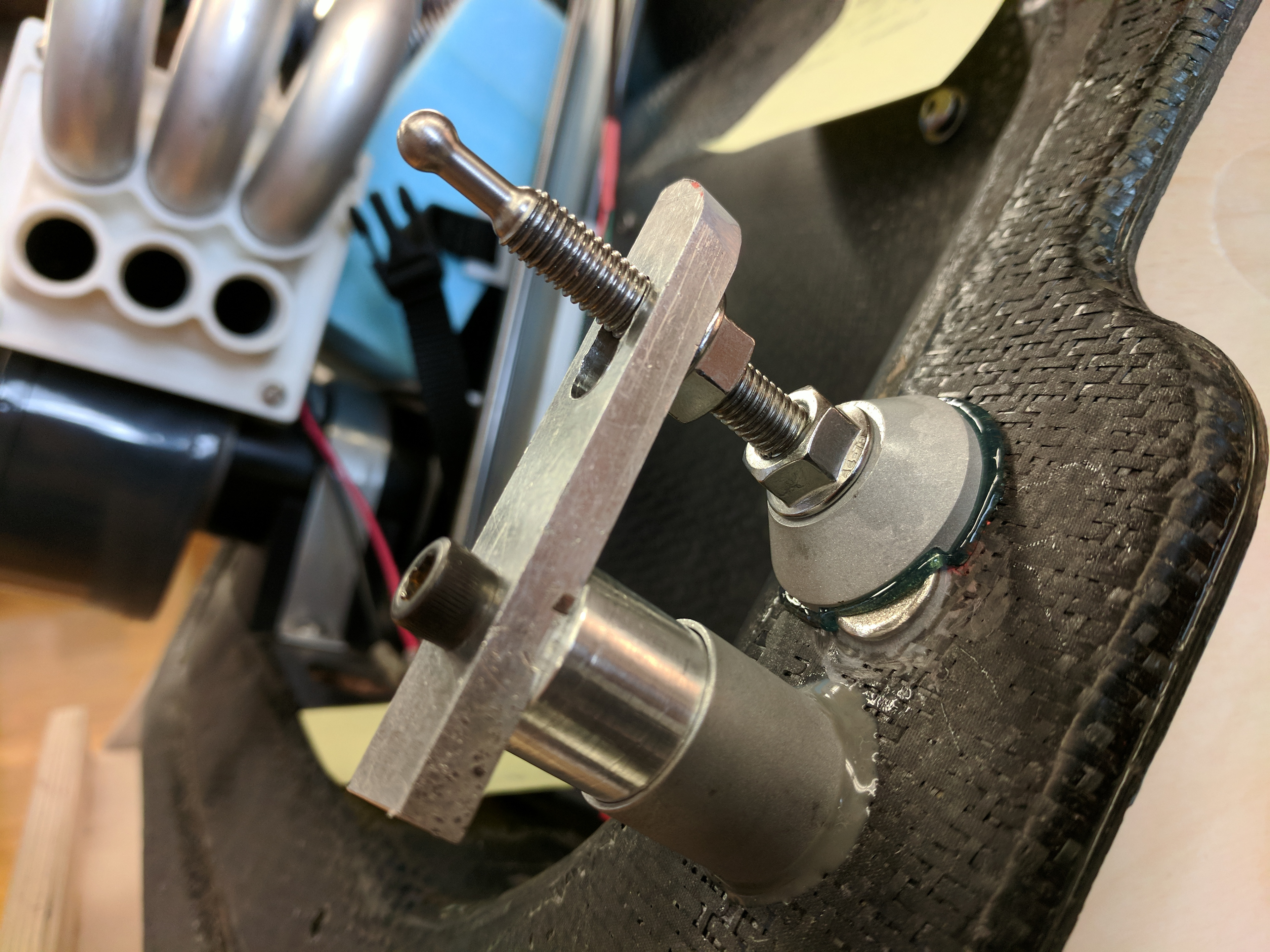
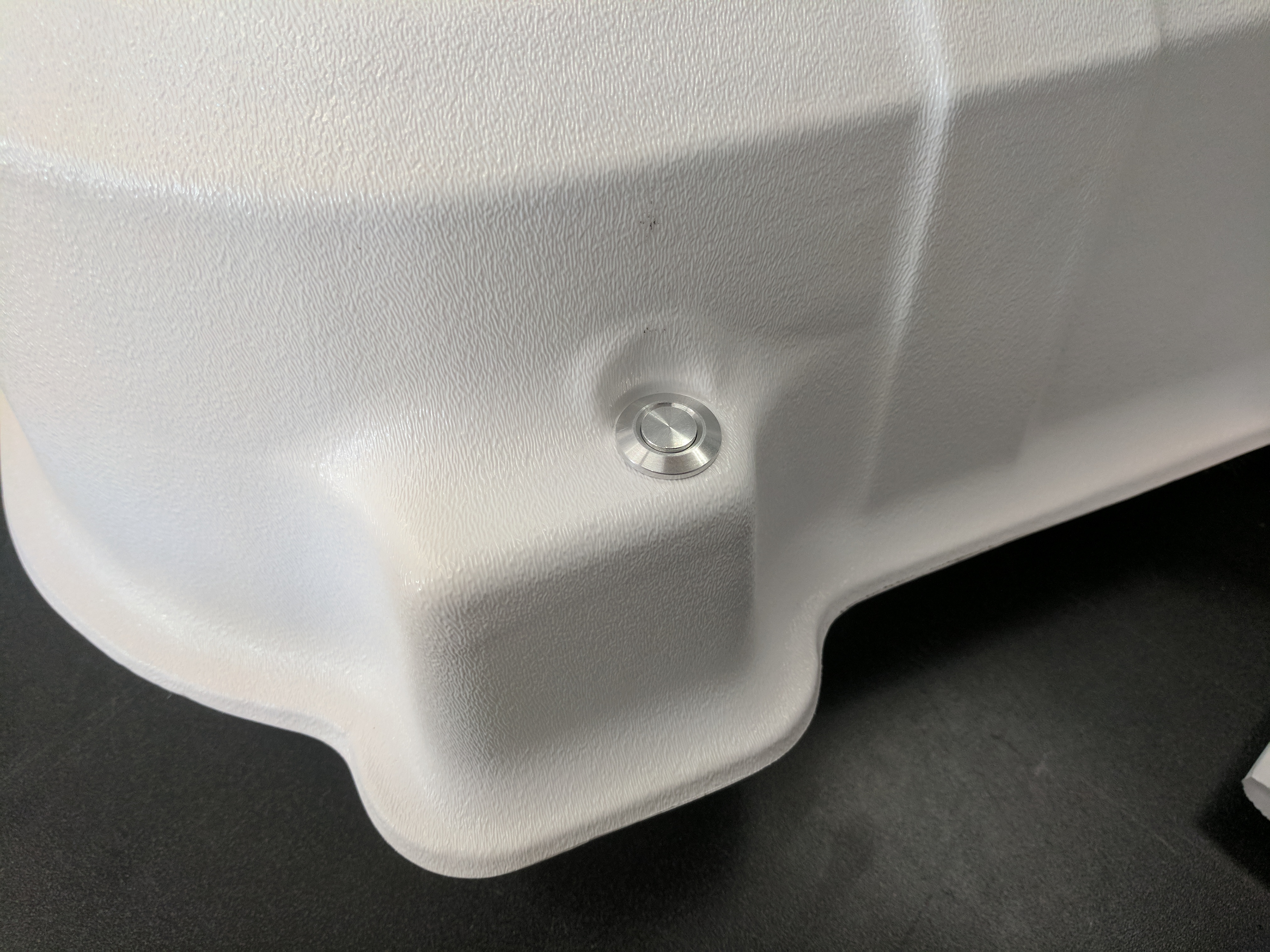
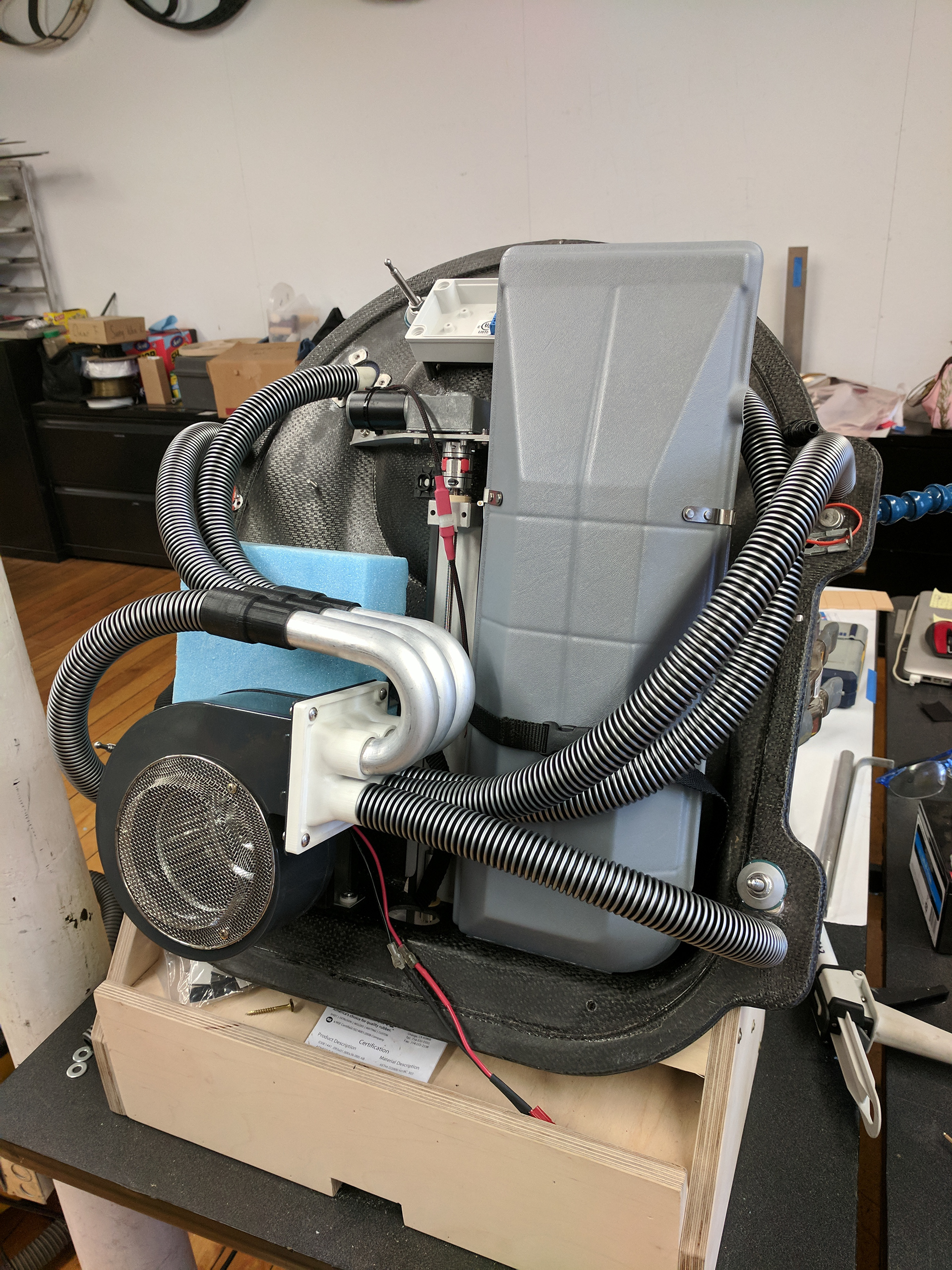
Final Results
The project was used for HI-SEAS VI mission simulation in Hawaii to be tested in hot environment, and was also sent to Iceland to be tested in cold extreme environment.
Related Articles:
"Scientists Test Mars Spacesuit by Climbing a Glacier in Iceland"
https://www.space.com/mars-spacesuit-prototype-iceland-glacier-test.html
https://www.space.com/mars-spacesuit-prototype-iceland-glacier-test.html
"MS1 Mars Simulation Suit Prototype is Closest you can Get to Mars on Earth"
https://www.syfy.com/syfywire/ms1-mars-simulation-suit-prototype
https://www.syfy.com/syfywire/ms1-mars-simulation-suit-prototype